On the Importance of Electroplating on Printed Electronic Tobacco Circuit Board PCB
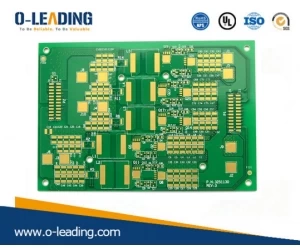
On a printed circuit board, copper is used to interconnect components on the substrate, although it is a good conductor material for forming the pattern of the conductive path of the printed circuit board, but if exposed to the air for a long time, It is easy to lose luster due to oxidation and lose weldability due to corrosion. Therefore, various techniques must be used to protect copper traces, vias, and plated vias, including organic paints, oxide films, and plating techniques. Organic lacquering is very simple to apply, but it is not suitable for long-term use due to changes in its concentration, composition and curing cycle, and it can even lead to unpredictable deviations in weldability. The oxide film protects the circuit from corrosion, but it does not maintain solderability. Electroplating or metal coating processes are standard operations that ensure solderability and protect circuits from corrosion and play an important role in the manufacture of single-sided, double-sided and multilayer printed circuit boards. In particular, plating a layer of weldable metal on a printed wire has become a standard operation for providing a solder resist to a copper printed wire.
The interconnection of various modules in an electronic device often requires the use of a printed circuit board (PCB) header with spring contacts and a printed circuit board with connection contacts designed to match the design. These contacts should have a high degree of wear resistance and a very low contact resistance, which requires a thin layer of metal to be plated, the most commonly used metal being gold. In addition, other coating metals can be used on the printing line, such as tin plating, plated soldering, and sometimes copper plating in certain printed wiring areas.
Another coating on copper lines is organic, usually a solder mask, which is coated with an epoxy film using screen printing techniques where soldering is not required. This process of coating an organic solder resist does not require electronic exchange. When the board is immersed in the electroless bath, a nitrogen-tolerant compound can be attached to the exposed metal surface without being absorbed by the substrate. .
The precision technology required for electronic products and the strict requirements for environmental and safety adaptability have led to considerable progress in electroplating practice, which is clearly reflected in the manufacturing of multi-substrate technology with high complexity and high resolution. In electroplating, a high level of electroplating has been achieved through the development of automated, computer-controlled electroplating equipment, the development of highly sophisticated instrumentation for chemical analysis of organics and metal additives, and the emergence of techniques for precise control of chemical reaction processes.