How to improve the thermal reliability of PCB circuit board?
o-lead
o-leading.com
2018-07-10 15:01:05
How to improve the thermal reliability of PCB circuit board?
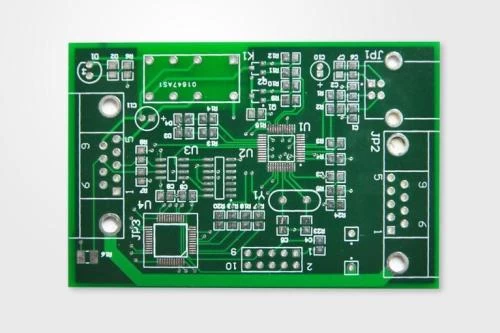
Thermal analysis
Thermal analysis in lamination process can help designers determine the electrical performance of PCB components(PCB factory who export the goods to Europe) and help designers determine whether the components or circuit boards will burn out due to high temperature. Simple thermal analysis is only used to calculate the average temperature of the circuit board. The accuracy of thermal analysis ultimately depends on the accuracy of the component power consumption provided by the circuit board designer.
Thermal analysis in lamination process can help designers determine the electrical performance of PCB components(PCB factory who export the goods to Europe) and help designers determine whether the components or circuit boards will burn out due to high temperature. Simple thermal analysis is only used to calculate the average temperature of the circuit board. The accuracy of thermal analysis ultimately depends on the accuracy of the component power consumption provided by the circuit board designer.
Weight and physical size is very important in many applications, if the components of the actual power consumption is small, could lead to the design of safety coefficient is too high, which makes the design of the circuit board do not tally with the actual or too conservative element power consumption value as according to thermal analysis. By contrast, is also more serious thermal design safety coefficient is too low, and the components of the actual runtime temperature is higher than analysts predict, such problems generally to add radiator or fan for cooling circuit board to solve. These external accessories adds cost, and extend the manufacturing time and join in the design fan will also bring unstable factors to the reliability, so the PCB board mainly adopts active rather than passive cooling way (such as natural convection, conduction and radiation heat).
Simplified circuit board modeling
Before modeling, analyze the main heating devices in the circuit board, such as MOS tube and integrated circuit block, which convert most of the lost power into heat when working. Therefore, these devices need to be considered when modeling.
Before modeling, analyze the main heating devices in the circuit board, such as MOS tube and integrated circuit block, which convert most of the lost power into heat when working. Therefore, these devices need to be considered when modeling.
In addition, also consider circuit board substrate, as a wire coated copper foil. , they not only have the effect of the conductive in the design, also have the effect of heat conduction, its thermal conductivity and heat transfer area is big PCB board is an integral part of electronic circuit, its structure by epoxy resin substrate and as a conductor of copper foil coating. The thickness of epoxy resin substrate is 4mm, and the thickness of copper foil is 0.1mm. The thermal conductivity of copper is 400 W/m ℃), and the thermal conductivity of the epoxy resin was only 0.276 W/(m ℃). Although the added copper foil is very thin and thin, it has a strong thermal guidance effect, which cannot be ignored in modeling.